Removing a Stuck Pitman Arm
When replacing a pitman arm, the nut and lock washer that retain the
arm to the steering gear usually come off easily with the properly
sized socket. If a proper socket is not avaliable, an axle nut socket
intended for servicing front wheel drive cv axle assemblies will often
work in a pinch (30mm, 32mm, 34mm, 36mm, etc.).
The nut that retains the rotating stud on the pitman arm to the center
drag link usually comes off without too much effort too. From the
factory, the later crown vics use a nylon based system to lock the nut
in place. But many aftermarket replacements use a castellated nut with
a cotter pin instead.
However, actually sliding the pitman arm off of the steering gear
output shaft is sometimes rather challenging. According to the ford
service manuals, simply place the appropriate pitman arm puller on the
pitman arm, tighten the pressing bolt, and the arm will pop right off.
However, this is often not that case with a pitman arm that has been in
place for several years.
In this particular case, the pitman arm was seized onto the gearbox and
tightening down the forcing bolt only resulted in broken pitman arm
pullers. The ford service manual does not have a procedure for this
particular complication. But in the field, there are a few possible
solutions:
-Heat the arm with an acetylene torch, and then use the puller. But
this is likely to damage the hydraulic seals inside the box along with
the output shaft bearings.
-Bang a large balljoint "pickle fork" seperator in between the gear and
the pitman arm with a big sledge hammer. Also likely to damage the
output shaft bearings inside the box.
-Use an angle grinder to cut a notch in the pitman arm around where the
sector shaft passes through the pitman arm.
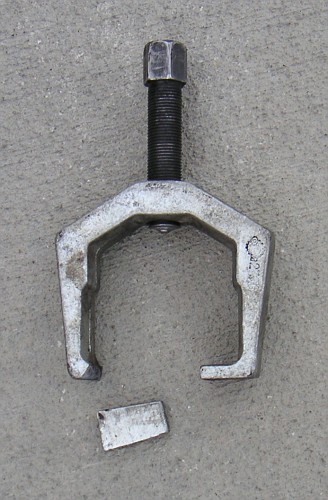
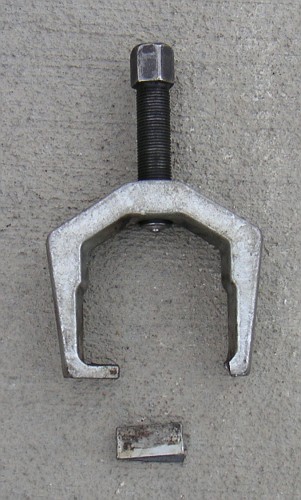
For this project, the method of cutting a notch in the pitman arm is
going to be used as it's the least likely to damage the gear box.
So here's the box with the stuck pitman arm.
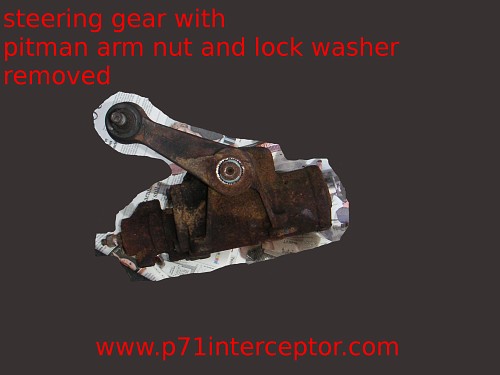
Here's the gearbox with the notch cut into it near the sector shaft.
In this case, the grinder cut a deep notch into the arm without cutting
into the sector shaft at all.
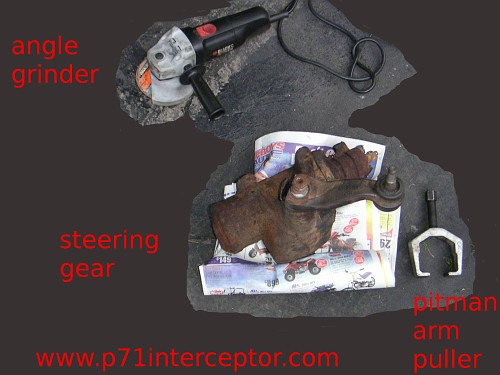
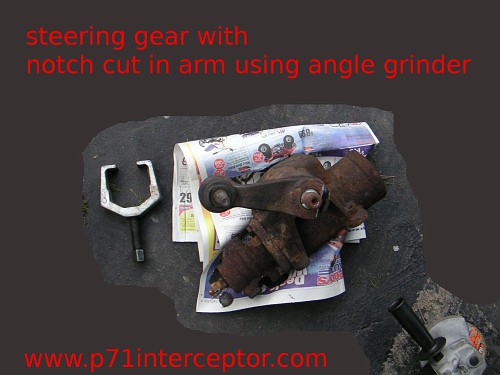
The arm now popped right with a pitman arm puller after a pressure
relief slot was cut into the metal.
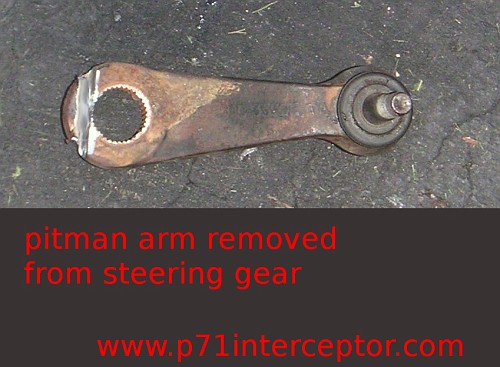
Here's the gearbox that previously had a pitman arm that wouldn't come
off
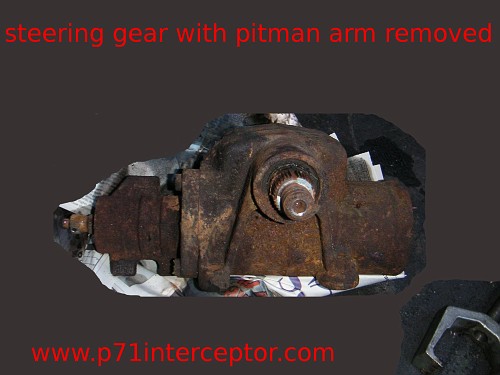
And here's the tool that was used for the job. A 4.5" electric angle
grinder with a thick abrasive metal cutoff wheel.
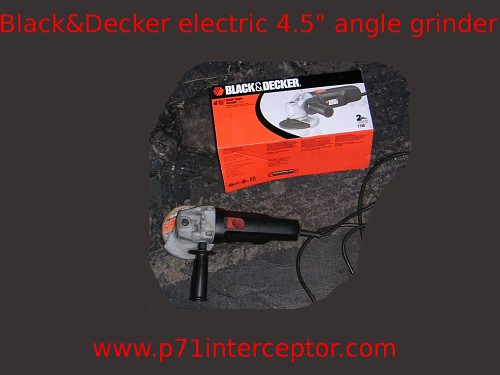
The electric angle grinder makes easy work of pitman arm. But it also
makes lots of sparks and dust in the process. So make sure to wear eye
protection
and a dust mask too.
There was some localized heating to the arm using the angle grinder.
But this heat was minimal compared to the flame of a 4000+ degree
oxygen/acetylene torch.
Some people have commented that there are stronger pitman arm pullers
that are less likely to fail when removing a pitman arm
than the cheapie autozone $10 one pictured above. While this is true,
there are also some pitman arms stuck on the sector shaft so good that
you can break even the best pitman arm pullers.
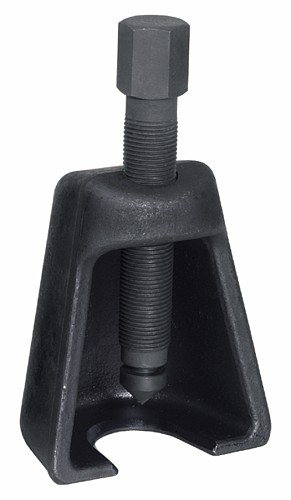